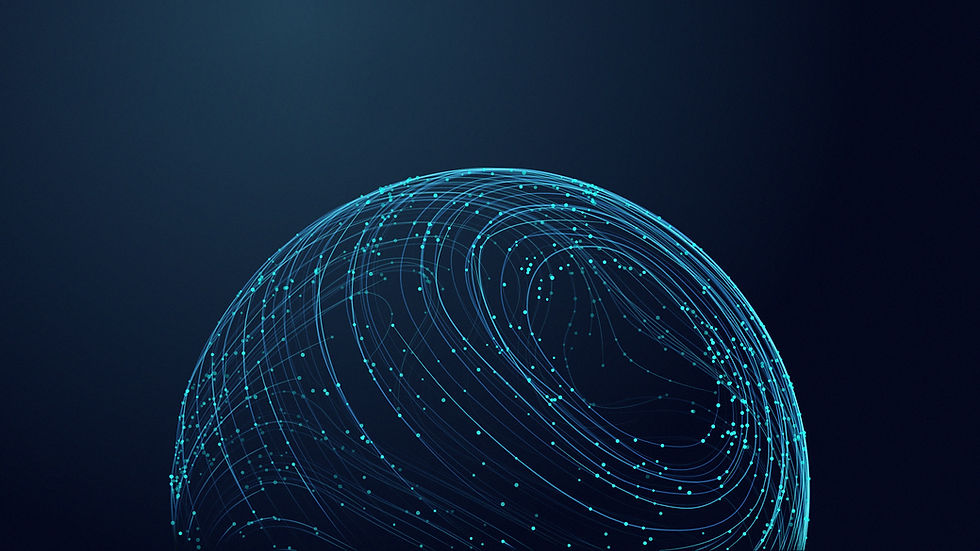
I'M
Michael Valdez.
Data Analytics/
BS in HR Analytics/
Driven Collaborator

michael​.jose.valdez@outlook.com
Feel free to reach out for further connection.
Everywhere I go, I strive to make an impact. I am driven to see change for the better. This isn't just about data. It's about making an actual difference. It's about seeing the seed of an idea bloom into a beautiful impactful result. As a Data Analyst and Parts Manger at Ford, I do this everyday. As a strong problem solver, I couple initiative, communication and drive to make an impact and experience results.
Data, whether simple or advanced, should simply solve a problem .

01 PORTFOLIO
02 Experience
2023 - PRESENT
Ford
2016 - 2023
Data Analyst/Parts Manager
-
Created business analysis reports by developing inventory dashboards in Excel, improving storage efficiency and reducing time to charge out shop supplies by 40%.
-
Led process improvement initiatives by analyzing and organizing key storage and sales workflows, resulting in the successful sale of old inventory that had been stored for years.
-
Applied project management techniques to streamline daily processes by researching and integrating DMS features, enhancing software capabilities and improving team productivity.
-
Collaborated on requirements gathering to convert Ford PDF document into a functional Excel file, enabling quick search of Ford base numbers and reducing team member downtime.
Target Distribution GSCL
Team Member Trainer/
Lead Warehouse Worker
-
Led project management efforts to increase daily productivity, successfully holding two back-up lead positions simultaneously and contributing to overall team efficiency.
-
Streamlined business processes by creating a start-of-shift dashboard for team members, reducing first scan time by 50%, improving operational efficiency.
-
Conducted business analysis to identify a gap in the capacity team member database process and initiated a partnership with Quality Operations Managers to create a Microsoft Excel database template, helping the ICQA team identify and resolve quality errors.
-
Led process improvement initiatives by initiating and managing an early start capacity team of 6-10 members to address capacity constraints during peak season, optimizing resource allocation.
-
Engaged in cross-functional communication through daily check and adjust meetings with leadership, ensuring the building's capacity needs were met, and facilitating efficient freight flow from Inbound to the Warehousing department.
-
Developed data visualization reports to track capacity trends, providing the production manager with actionable insights into daily capacity performance and enabling informed decision-making.
-
Created and presented process improvement strategies to peers and middle leadership, successfully implementing a new capacity strategy that is currently utilized by approximately 40 team members.
-
Provided clear communication and feedback to warehouse team members, addressing performance gaps and delivering mentorship to ensure role expectations were met.
Recommendations
